All made of stainless steel, with polished inner and outer membrane shells;
Inlet method: Inlet at both ends (Type A), inlet on both sides (Type B);
Structure: Standard spare parts, easy and fast disassembly;
Sealing: Tested for pressure resistance;
Organizational structure at both ends: clamp type, flange type, built-in type.
The materials used in reverse osmosis membrane module pressure vessels mainly include fiberglass, stainless steel, engineering plastics, etc. The application working pressure range is usually from 150psi (1.0MPa) to 1000 psi (6.9MPa), and fiberglass is mainly used in medium and high pressure applications.
Fiberglass is composed of glass fibers or their fabrics and synthetic resins. People can change the content and distribution of glass fibers. Obtain fiberglass with different strengths and elastic properties within the range to withstand different loads.
Through reasonable selection of materials and appropriate processes, fiberglass has good stability to various low concentration acid, alkali, salt media and solvents.
When developing pressure vessels with reverse osmosis membrane components, strict screening was carried out on the process of the inner lining layer to ensure the sealing, non toxicity, non pollution, and long-term non corrosive requirements of the reverse osmosis membrane pressure vessel.
Optimized the design of the structural layer and the layer at the end retaining ring groove of the pressure vessel to ensure structural integritygoodIt has a long service life and good dimensional stability under working pressure. The concentrated water inlet has also been optimized to ensure the variability of the interface during installation.
Precautions for using pressure vessels:
1. Ensure that all components on the pressure vessel have been correctly and reliably installed before use;
2. Ensure that pressure vessels are horizontally supported and securely fixed at the recommended span (s) by the manufacturer;
3. Ensure that the fixing and piping connections of the pressure vessel have flexible and cushioned space to accommodate the radial and axial increase of the pressure vessel under pressure
Impact;
4. Ensure that the system device provides overpressure (greater than 105% of the design pressure) protection for the pressure vessel;
5. Ensure regular inspection of end plates and piping interfaces, and timely replacement of corroded or damaged components;
6. Ensure that all rubber seals and pressure vessel inner surfaces have been properly coated with lubricants such as glycerin, dishwashing detergent, etc. before use;
7. Do not attempt to disassemble any components on the pressure vessel under pressure;
8. No rigid fixation or connection shall be made to pressure vessels;
9. Do not operate the pressure vessel downstream without installing a thrust ring;
10. Do not use pressure vessels beyond their usage conditions;
11. Pressure vessels are not allowed to have any leakage or end plate components that are constantly in a damp state during use.
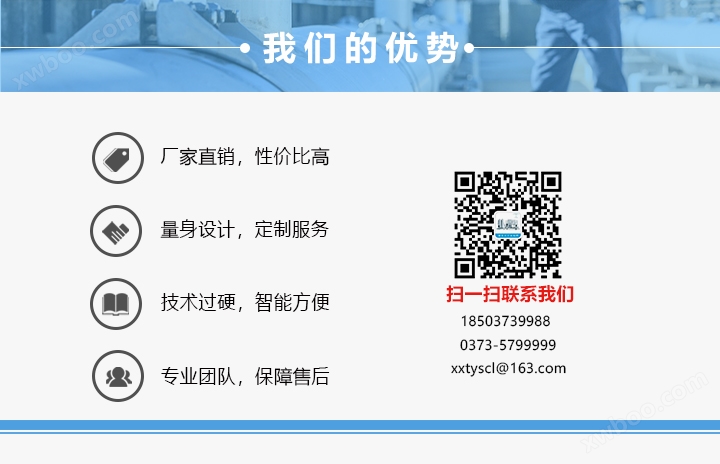